The due diligence dilemma: Can qualification teams navigate the complexity of Europe's supply chain legislation?
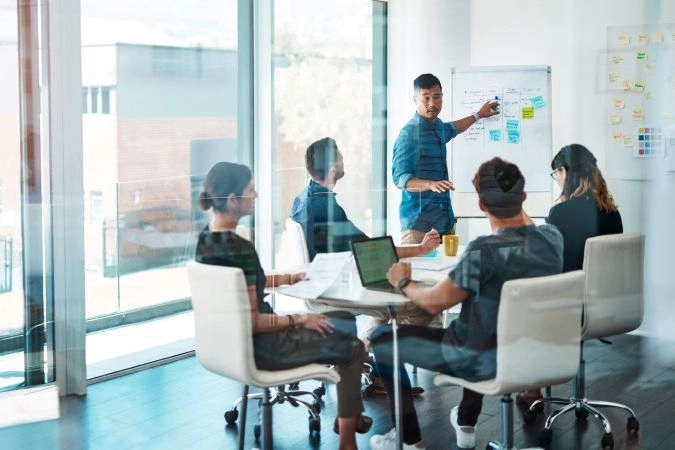
The global trade landscape is undergoing a seismic shift, with the EU's Supply Chain Due Diligence (SCDD) legislation emerging as a tectonic force. This ambitious initiative, poised for implementation in stages starting in 2024, aims to hold companies accountable for the environmental and human rights practices of their entire supply chains, no matter how geographically distant. But in this grand undertaking, a critical question arises: can traditional supply chain qualification teams effectively navigate the complexities of this new landscape?
For years, qualification teams, often nestled within shared service centres, have played a crucial role in vetting potential suppliers. They pore over questionnaires and assess responses for compliance with company standards. However, the SCDD's expansive scope – encompassing human rights, environmental protection and conflict minerals – demands a far more nuanced approach, particularly for qualification teams accustomed to focusing primarily on financial stability and operational efficiency.
The expanding risk matrix
The SCDD introduces a vast new matrix of risk factors. Qualification teams must now delve into areas like forced labour, child exploitation, anti-corruption, information security, resource depletion and pollution – subjects often requiring specialised expertise beyond their traditional skillsets. This complexity can overwhelm under-resourced teams, potentially leading to superficial assessments that miss crucial red flags. In many cases, these teams have not been able to scale themselves and their knowledge to address the complexity.
The translation trap
In today's globalised world, many suppliers operate in languages different from the qualification team's native tongue. This linguistic barrier can create significant hurdles. Reliance on questionnaires translated by potentially unreliable services or machine translations can lead to misunderstandings, misinterpretations and,ultimately, inaccurate assessments of risk. Of course, it is not only the questionnaire responses that require translation – so too do the underlying documents that are uploaded as part of the application process.
The cost-cutting conundrum
In the quest for cost savings, some companies outsource their qualification teams to shared service centres in low-cost regions. While this might seem financially prudent, it introduces additional challenges. These centres often lack the regional knowledge and cultural understanding necessary to effectively assess risk in diverse supplier locations. Moreover, the cultural distance between the qualification team and the suppliers can create communication barriers and hamper the ability to build trust – a critical factor in obtaining reliable information. While these teams are sometimes independent, they are often staffed with procurement professionals who may not understand all of the legal and compliance best practices of the selection and qualification process.
The risks of superficial scrutiny
The reliance on self-assessment questionnaires (a common practice in traditional qualification) is particularly problematic under the SCDD. With the potential for greenwashing and manipulation lurking around every corner, these questionnaires alone cannot uncover hidden ethical issues. Independent, in-depth audits conducted by qualified experts, often beyond the scope of shared service centres, are essential to pierce through the veil of self-presentation and expose potential violations. While this may not be appropriate or possible for all suppliers, an in-depth audit would be appropriate for some.
The path to responsible sourcing
So, how can companies ensure their qualification teams are equipped to navigate the complexities of the SCDD? The following are some key steps.
• Upskilling and training
Invest in training programmes that equip qualification teams with human rights, environmental sustainability and conflict minerals expertise. This includes developing language skills and cultural understanding relevant to the company's supplier network.
• Prioritisation and risk-based approach
Implement a risk-based approach, focusing resources on high-risk suppliers and sectors identified through detailed risk mapping and analysis. This ensures efficient resource allocation and prioritises the most critical areas for due diligence. While companies say they apply a risk-based approach, most do not apply such an approach in practice. They ask for the same information from the same suppliers without any significant difference.
• Collaboration and partnerships
Partner with independent auditors with expertise in specific risk areas and regions. This leverages external expertise and ensures a more comprehensive assessment of supplier practices.
• Technology and automation
Utilise technology to streamline data collection, analysis and reporting. This can free up human resources for more complex tasks and improve the overall efficiency of the due diligence process. Consider how AI can review and conduct an analysis of the submitted data.
• Transparency and communication
Foster a culture of transparency and open communication within the organisation. Encourage employees to report potential ethical violations and provide clear channels for raising concerns about suppliers.
The SCDD is not just a legal obligation; it's a wake-up call for companies to reimagine their approach to supply chain due diligence. The days of relying on superficial questionnaires and outsourced qualification teams are over. Companies must invest in building agile and competent teams equipped to navigate the complexities of the new regulatory landscape. This requires a commitment to upskilling, risk-based prioritisation, strategic partnerships and technological innovation. Only then can companies fulfil their responsibility for ethical sourcing and build resilient, sustainable supply chains for the future.
This is not just a call to action for companies; it's a call for collective responsibility. Consumers, investors and policymakers must hold companies accountable for their due diligence practices, incentivise responsible sourcing, and support initiatives that promote ethical and sustainable trade. Together, we can build a world where supply chains are not conduits for exploitation but engines of positive change driven by a shared commitment to human rights and environmental protection.